高炉冶炼产生高温液态熔渣(1350-1500℃),作为钢厂产生的主要固废之一,伴随着钢铁工业的不断发展,其产生量是巨大的。据统计,2021年我国高炉生铁产量约8.68亿吨,产生熔渣约3亿吨。采用水冲渣工艺将高炉炉渣粒化后作为水泥原料,是高炉炉渣固废资源化利用的一个有效途径。
长期以来,渣水分离主要采用传统底滤法工艺或机械法工艺。如何以最佳方式完成炉渣粒化、处理水冲渣工艺产生的蒸汽并实现渣水混合物的高效分离,对于钢铁行业的绿色发展和我国的循环经济具有非常重要的意义。很多新建、改建高炉工程,由于受场地限制,无法选用占地面积较大的传统底滤法工艺,而机械法工艺又存在投资成本高、维护工作量大等弊端,市场迫切需要一种新的水渣处理工艺解决方案。面对这些问题和需求,中冶京诚勇于担当,开启了环保底滤法高炉炉渣处理技术的创新发展之路。
2008年,中冶京诚在业内首创了环保底滤法高炉炉渣处理技术,并获得了发明专利。翌年,便在江阴兴澄特钢3200立方米高炉工程完成了该技术的首次成功应用。2010年,中冶京诚首次将该技术成功应用于传统底滤法改造工程。2015年,又首次将该技术成功实施于机械法改造工程。核心专利荣获2018年度中国专利优秀奖。历经不断的技术提升,2020年中冶京诚首创智能抓渣、蒸汽回收系统,应用效果广获好评,至此完成了第二代环保底滤法高炉炉渣处理技术的开发应用。
十几年来,环保底滤法高炉炉渣处理技术被广泛应用于江阴兴澄特钢、马钢、包钢、河钢唐钢新区等35家钢铁公司及唐山凯源镍铁合金生产线,近80套水渣系统,在业内获得广泛认可。2022年经行业专家科技成果评价,项目成果总体达到国际先进水平。
中冶京诚环保底滤法高炉炉渣处理技术创新及应用效果:
首创新型底滤法炉渣处理工艺
新型底滤法炉渣处理工艺,围绕高炉炉渣粒化环节和过滤环节的渣、水、汽进行研究开发,高效结合粒化系统、过滤系统、抓斗起重机、冷却塔、储水池、循环泵组,首创解决了传统底滤法水淬粒化易爆、含水量高、占地面积大等问题,通过提高过滤速度和单位过滤面积的过滤能力,节省过滤池占地面积约40%。
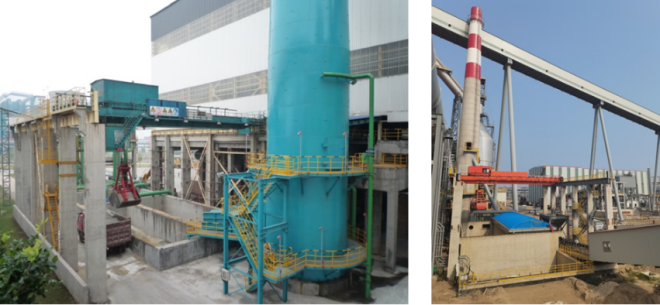
环保底滤法高炉炉渣处理技术现场应用情况
蒸汽回收系统
开发粒化消白塔,在粒化消白塔的底部设置粒化池完成炉渣粒化,在粒化消白塔的上部设置蒸汽回收系统;开发过滤池蒸汽回收系统,在过滤池上设置移动蒸汽罩,对正在冲渣的过滤池进行封闭处理,通过蒸汽回收管道引出过滤池蒸汽进入粒化消白塔。通过蒸汽回收系统实现高炉水渣工艺的环保消白和水资源循环利用,吨渣耗水量从传统底滤法的1.05吨降至0.85吨。
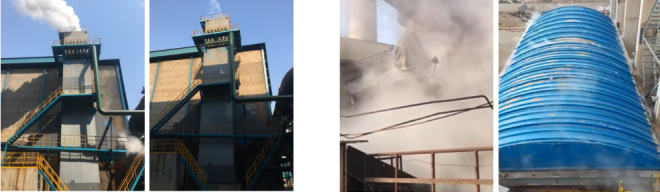
消白前后对比
高效长寿渣水分离系统
开发高效长寿渣水分离系统,合理匹配梯级高效过滤设施、模块化高效过滤结构与循环泵组,实现“无水”抓渣,解决了渣水分离不彻底和过滤水悬浮物含量高的问题,实现过滤水悬浮物含量<8mg/L、成品水渣含水量<11%,大幅减少水资源的浪费。
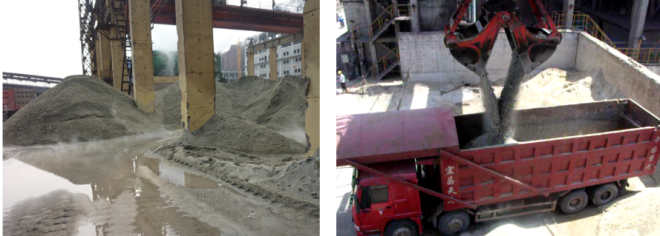
传统带水抓渣和 “无水”抓渣现场对比
基于3D扫描识别技术的智能抓渣系统
开发基于3D扫描识别技术的智能抓渣系统,实现快速抓渣清理作业,解决人工操作抓斗起重机作业环境恶劣、生产效率低的问题,提高作业效率约15%。
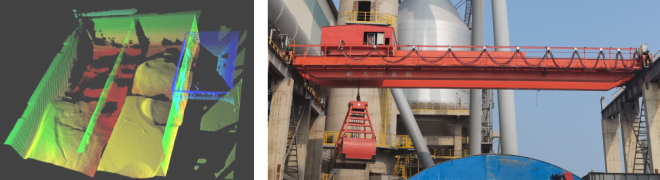
过滤池三维数据演示/无人值守智能天车
综合数据显示,与机械法相比,采用环保底滤法高炉炉渣处理技术,过滤水悬浮物含量从~1000mg/L降至<8mg/L,成品水渣含水量从>17%降至<11%,吨渣耗水量从1吨降至0.85吨,吨渣耗电量从15.2度降至11.9度,维护成本从350万元/年·套降至50万元/年·套。
中冶京诚环保底滤法高炉炉渣处理技术解决了高炉炉渣处理领域的多项技术难题,在减少投资、节省占地、节水、节电、减少维护费用、环保消白等方面具有明显优势,符合我国生态文明建设和绿色发展的需求,是新建、改建各级别高炉水渣设施的最佳选择。