9月12日,由中国金属学会和河钢集团有限公司联合主办的首届(2023)中国钢铁工业数字化发展高端论坛在河北唐山成功召开。会议特邀行业著名院士学者就钢铁工业的数字化发展指导交流并做专题学术报告,邀请国家相关部门、科研院所、宝武、鞍钢、河钢等典型钢企以及国外知名企业共20位专家共同分享近年来钢铁行业数字化、智能化转型过程中所取得的突出进展,就热点、难点及关键共性技术问题进行深入交流研讨。
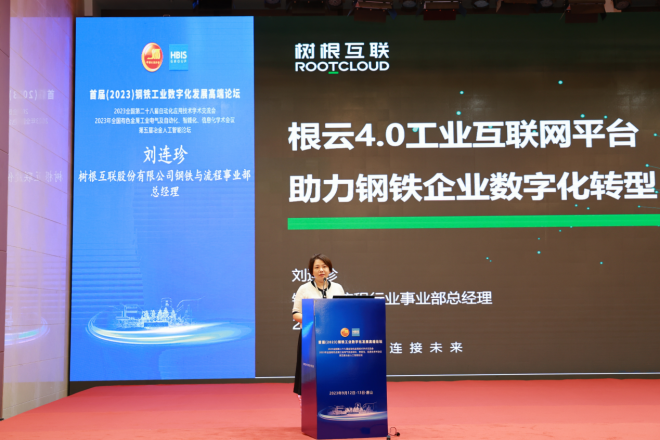
会上,树根互联钢铁与流程行业事业部总经理刘连珍以“根云4.0工业互联网平台助力钢铁企业数字化转型”为题发表主题演讲,向与会嘉宾分享树根互联在钢铁冶金制造企业数字化转型过程中的方案案例。
“如何将业务模式、自动化、流程数字化、数据分析综合在一起,管理手段又将如何细化、融合,寻找新的突破口?构建多维度的企业增长方式,是钢铁行业面临的主要难点。”对于未来钢铁企业智能工厂的建设方向,刘连珍认为需要聚焦发力两个方面,一是包括运营敏捷化和场景化推进在内的“看得见”,另一个则是包含平台化思维和数据驱动在内的“看不见”。
其中,在“看得见”方面,运营敏捷化需要围绕工厂全价值流进行刨析优化实现钢厂运营数字化、透明化,支撑企业卓越运营;场景化方面,则需要系统梳理钢厂价值流堵点及痛点,切实解决问题和参考行业标杆对新技术与业务融合的可行性进行深度评估以创新技术。
在“看不见”方面,平台化思维指的是构建工厂的统一数字化底座,将多套老旧系统架构逐步演进过渡到统一平台,打破传统信息孤岛;数据驱动指的是打通钢厂工序内及跨工序数据链,支撑高价值数据场景落地,通过数据量化指标、构建模型、提升运营绩效并不断迭代优化。
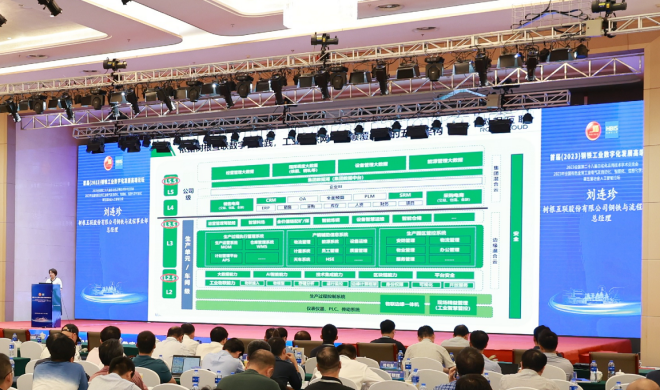
“平台是钢铁企业快速响应内外部需求实现敏捷创新的重要工具,也是核心能力的内聚。工厂智能化改造及运营推进,背后依靠的是‘看不见’的推手。”刘连珍介绍道,树根互联依托在钢铁冶金等跨行业、跨领域的丰富数字化实战,将工业互联网平台与钢铁企业的五级架构进行了很好的融合。通过建立统一的数据标准和数据格式接口,可以将每个层级的独立系统汇聚在根云4.0平台,实现设备的互联互通和数据的共享。
将OT与IT数据融合,根云4.0平台目前已构建了1个连接通道+1个智能基座+N个智慧应用的工业互联网平台应用服务体系。其中,连接通道基于百种协议实现海量工业数据泛在连接;智能基座构建从“感知”到“认知”的服务能力,实现OT数据与IT数据结合,服务各类应用;智能应用实现数据可视化,多维度立体分析,以数据快速、动态驱动决策。
据介绍,树根互联以价值驱动的基于工业互联网架构新一代数字化平台,为钢铁企业提供从企业数字化转型规划到落地的创新解决方案。
截至目前,树根互联已为国内多家钢铁有色、建材企业服务,为钢铁企业践行新发展理念,推动高质量发展提供数字底座支撑。
在国内知名建材企业的可视化数字工厂项目中,该企业在全国各地拥有100多个工厂,树根互联基于根云4.0平台将其每个工厂的每条产线进行链接,通过根连工业软件与硬件采集工厂侧设备数据,实现OT数据的一体化管控;通过云视界产品实施,实现生产工艺远程实时可视和远程参数下达;通过AI算法实现对工厂安全类(安全帽、工服、超速、地磅闯入)、生产异常(石膏断料、玻纤断料、二控乱板、三控乱板)实时监控与预警。
在华北某大型钢铁公司的智慧集控运营指挥中心项目中,针对该集团公司和下属制造基地对精益管理的需求,树根互联借助根云4.0平台实现基础设施建设的连接,通过数据中台的系统覆盖进一步完善指标报表体系,结合IT及OT数据实现产线质量的数据分析、降低质量成本,根据不同场景实现整体集中调度运营,最终实现集中化操控和集中化运营。2022年,该企业被评为“数字领航”企业,成为制造业数字化转型的标杆案例。
在西北某镍钴产业集团的大板镍数字化工厂项目中,针对客户物流管理时效性差、检验检测准确性低、设备维修溯源困难三大痛点,树根互联为其打造“基于IOT融合的生产管控系统”,全面提升成品车间产效率、电镍产品质量与可靠性。项目投入使用后,有效降低10%的非计划性停机事故,全年镍产品提升30%产量;通过优化收、储、运业务环节,提升车间物流动线效率30%以上,节约能源、运输费用超百万元。
“未来的制造业,将在离线的物理世界基础上升级叠加在线的数字世界,从而能够广泛的利用新一代信息数字技术,推动制造业全面升级。随着生产要素的网络化连接,生产要素和生产过程的数字化,生产和管理决策的智能化提升,制造模式也朝着平台化在线实时智能协同演进。”刘连珍如是说道。