今年以来,河钢工业技术紧跟集团绿色转型和绿色电力需求挑战的决策部署,加快推进绿色交通技术应用和绿色低碳产业布局,聚焦“打造钢铁产线极致能源流”目标,以节能储能为发力点,发挥自身技术和业务的“双优势”,积极寻求质量与稳定、高效的平衡点,全面提升能源管理水平,不断推动节能、降耗,协同增效。公司牵头推进能源管控系统建设,围绕空压机自动负荷调控,冶金产线余热发电,循环水系统改造等,实现装备的智能管控,实现打造能源流极致能耗。截至目前,唐钢公司铁前空压机站2#机电流从163A降低到了120A,4#机电流从160A降到150A;钢轧空压站1#机电流从162A降到118A,3#机电流从160A降到152A。
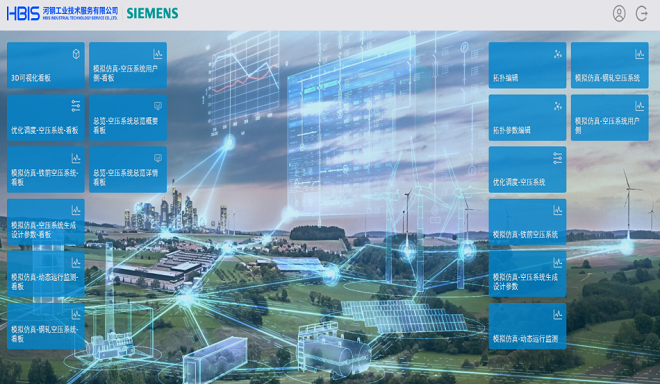
技术节能 撬动极致能效提升新价值
“系统运行稳定。铁前空压机站和钢轧空压站分别实现单台空压机节电率16.4%和16.1%,已经大大超出了之前预计的效果。”7月4日,河钢工业技术节能储能项目负责人高军在系统控制室屏幕前兴奋地说道。
由河钢工业技术联合唐钢公司动力部、河钢数字和西门子艾闻达等单位共同推进的空压机、余热发电汽轮机组数字化能源管控系统研发项目完成最终调试,在唐钢公司正式运行。该项目的实施,标志着集团加快推进极致能效取得突破进展。
“我们要坚定培植‘极致按需用能’的思维和定力,与技术人员一起,围绕高效率机组、高效益产线,深入优化煤气、蒸汽、水、电、气体等能源系统平衡,通过信息化、自动化手段,不断提升能源加工转换效率,实现效益最大化。”高军在项目研讨会议上说道。
该项目主要选用数字化能源管理系统软件iEMS作为实现工厂能源系统智慧化管理的工具和平台,旨在打造架构数字化的能源优化管理。通过对发电、煤气和水等各类能源介质系统进行全面梳理分析、顶层设计和系统优化,实施动态监测、实时仿真、回归分析、智能诊断,智能预测、优化决策,打造了智能控制优化系统、智慧燃烧专家系统、智能运行辅助、智能预警等智慧功能应用,实现对系统运行参数的实时分析调优,从而使整体系统的运行效果达到能效优化,节能降耗。
下一步,该公司将加快压缩空气系统集中群控智慧节能技术在全集团复制推广,预计每年为集团节电4000万度以上,降碳3万吨,节电效益2000万元以上,助力集团加快培育新的竞争优势。
绿电储能 拓展钢铁行业降碳新思路
在大河金属衡板包装公司的厂房附近,由河钢工业技术承建的衡板包装光充换检一体化绿色交通设施建设与运营项目正式开工,此项目标志着集团首个清洁能源绿电应用场景投建,正式开启集团绿电领域新赛道。
“储能,就如同能源领域的‘蓄水池’,它能够在能源供应过剩时将其储存起来,在需求高峰时释放,从而实现能源的高效调配。此次项目,是集团在绿电领域的一次新的探索和实践,我们要将储能绿电技术应用到为新能源物流车辆提供充换电服务的同时,还作为能源存储装置实现对用电负荷的削峰填谷,实现在确保厂区有序用电、安全用电的同时,实现用电费用和碳排放量大幅降低,预计每年节省电费支出140万元,减碳2400吨。”该公司储能项目负责人蔡颖新在项目启动会上激动的介绍道。
今年以来,该公司致力于成为河钢集团扩展清洁能源领域的实践者,大力推动以“双碳+能源+数字化”为核心,采用电化学储能等方式,提供成套储能技术解决方案,实现产线用电成本大幅降低。该公司联合华北电力、西南交大等高校,共同成立“能源技术创新中心”,发挥技术人才优势,聚焦“本质安全型储能电池”“V2G双向充电桩”“移动储能车”“车载电池箱安全防护终端”和“本质安全型PCS”等核心技术和产品开展研发,通过搭建虚拟电厂交易平台,利用储能可调控负荷参与电力市场辅助服务,以源网荷储等模式,突破隔墙售电等政策制约,加快推进绿电及绿色交通局面建设,实现大宗绿电对主体厂的直供电,提高集团绿电应用比例。
目前,该公司重点推进唐山、承德、张家口、衡水等区域的绿电及储能项目,建成投运后,可实现储能项目规模450MW/900MWh、光伏项目装机容量40MW、风电项目装机容量40MW,预计为集团每年节省电费支出7000万元,供发绿电1.4亿kWh/年,实现绿电项目减碳10万吨/年,助力集团绿色可持续发展。
河钢工业技术严格落实集团“高端化、绿色化、智能化”发展,加快由单纯生产型企业向“制造+服务”型企业转变,牢牢把握“实现极致能效提升”的工作要求,紧扣“把提高能源高效循环利用效率作为巩固提升节能减排水平的根本举措”这一主题,聚焦当下冶金行业极致能效提升的热点、难点和痛点,大力构建能源管理和利用体系,通过可再生能源和储能技术,完成新能源替代,实现成本和碳排放的“双降低”,为钢铁行业提供极致能效提升成套解决方案,为助推集团绿色转型发展作出新的贡献。(董明 刘雪辉)