中国冶金报 中国钢铁新闻网
通讯员 宋超 报道
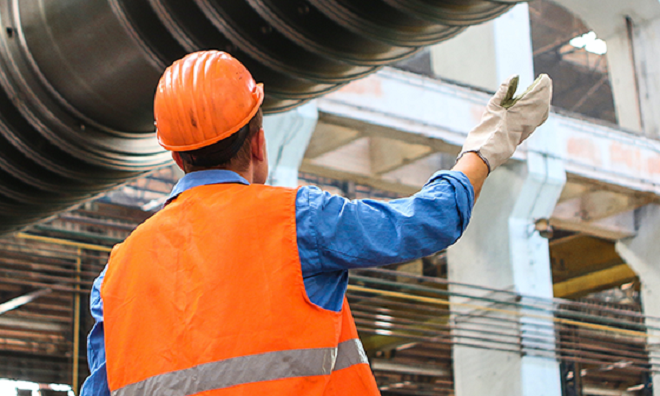
图为河钢邯钢宿永波。(聂伟杰 摄)
“我实施的‘提高转炉终点命中率’攻关,以应用转炉炼钢模型为基础,过程中有4项技术创新,包括开发冶炼静态模型……通过技术创新,钢水质量显著提升,仅物料消耗就可降低吨钢成本1.74元。”4月12日上午,在河钢集团邯钢新区炼钢厂“讲理想,比贡献”活动项目评审会上,该厂转炉炼钢工宿永波汇报道,而他针对提高转炉终点命中率的技术创新也获得了评委们的赞许。
扎根炼钢生产一线多年的宿永波是转炉炼钢技术和技能的多面能手,曾获全国钢铁行业技术能手、“河钢杯”第十届全国钢铁行业职业技能竞赛炼钢工比赛冠军、河北省技术能手等荣誉,他参与冶炼了高强工程机械用钢Q960系列、耐磨钢NM400—NM600系列等高端新产品20个。他始终坚信,推进低成本高质量炼钢,就要在不断总结和提炼前人成功经验的基础上,勇于主动作为,敢于技术创新。“我们要站在‘巨人’的肩膀上,为冶炼加入更多‘科技料’。”宿永波总结说。
4月15日9时许,邯钢新区炼钢厂转炉平台上,一炉钢水即将完成冶炼。此时宿永波正目不转睛地盯着出钢、喷粉过程。“取样检验后,炼钢渣中全铁含量16%,达到攻关目标。”听到这一消息,宿永波露出了欣慰的笑容。
面对此前炼钢渣中FeO比例升高,铁元素流失较多的情况,作为产线技术骨干的宿永波将“还原改质”作为减少铁元素流失、提高金属收得率的途径。他细致研究类似攻关案例,并与现场职工反复沟通,逐渐形成了自己的创新攻关方案。
宿永波决定在冶炼终点拉碳环节采取强搅拌工艺,降低炼钢渣中FeO含量;联合技术人员开发低成本高效压渣剂,在转炉终点破坏泡沫渣以提高不倒渣出钢比例,减少倒渣导致的高FeO含量炉渣流失;出钢过程向渣面投入低成本焦炭灰对炼钢渣中FeO进行还原,提高还原效率;在炉渣还原处理后,采用搅拌技术促进钢渣分离。
“通过实施一系列创新措施,炼钢渣中全铁含量降低了5个百分点,由此吨钢成本能降低10.89元,每年可创造经济效益2000多万元。”宿永波说。同时,围绕“降低渣中全铁含量”攻关,宿永波还完成了优化氧枪吹炼控制模式、优化底吹系统长寿命维护工艺等“配套工程”,成功提高了铁元素收得率。
“‘提高转炉终点命中率’是一个老课题,很多人都为之努力过。如今怎么让老课题焕发新生机,让看似到底的成本指标再‘破冰’,技术人员们需要反复琢磨研究。”4月11日中午,宿永波利用午休时间总结自己近期的攻关成果时写道。
此前,新区炼钢厂转炉一直存在终点命中率偏低的问题。“生产在变化,总会为改善指标提供突破口。既然找到问题,就离找到解决问题的方法不远了。”宿永波说。
此后,宿永波扎根炼钢一线,细致对比熔池碳含量和温度等指标变化,逐渐摸索出了几项创新措施。他优化冶炼静态模型,完善了冶炼过程中模型的判断逻辑,系统可根据一级数据自主判断一炉钢的开始、结束、倒炉、补吹、出钢、溅渣等冶炼节点,实现了实时显示散料加料时间、加料批量数据、枪位曲线、氧压流量曲线、炉气曲线,便于职工把控转炉冶炼状态。他联合技术人员开发转炉高效脱磷技术,改善转炉脱磷效果,提高了转炉终点命中率。
通过系统攻关,转炉终点命中率提升了10个百分点以上,吨钢钢铁料消耗成本降低1.74元。此外,围绕高效冶炼低碳钢种,他还提出了钢包底吹搅拌替代转炉内后搅技术,不仅缩短了冶炼周期、降低了转炉补吹比例,而且降低了铝制品脱氧剂消耗量。