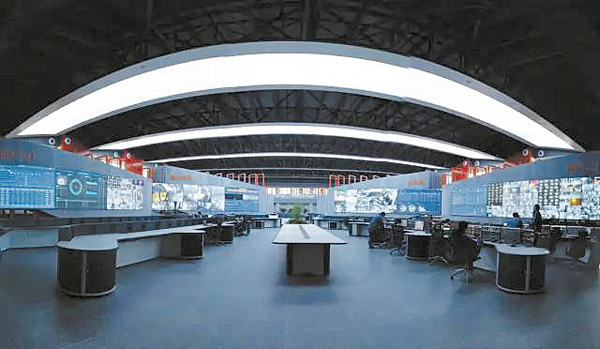
图为马钢炼铁智控中心
本报记者 陶海银
1月4日,中国宝武绿色发展·智慧制造大会在中国宝武马钢举行,由中冶赛迪集团总承包建设的马钢炼铁智控中心在大会上亮相,该中心代表了当前炼铁领域智能化的最高水平。
马钢炼铁智控中心是中冶赛迪深入贯彻落实习近平总书记关于“推动互联网、大数据、人工智能和实体经济深度融合”的重要讲话精神以及在马钢的调研指示精神,在智能制造领域打造的又一项行业样板工程。该项目基于中冶赛迪具有自主知识产权的水土云工业互联网平台的技术积淀,以大数据算法和智能化产品为内核,将数十项智能化先进技术首次植入钢铁制造,完成了钢铁行业产能规模最大、产线最多、集成度最高的智慧集控,实现智慧决策、智慧操控、智慧作业,大幅提高了钢铁企业生产效率、管理效益,树立了制造业转型升级、高质量发展的新标杆。
钢铁行业规模最大、产线最多、
集成度最高的智慧制造基地
马钢是中国宝武的优特钢精品生产基地,具备年产2000万吨钢配套生产能力。马钢炼铁智控中心对马钢铁区生产线进行全面集控,覆盖6座高炉、6台烧结机、4条焦化生产线、1台带式焙烧机和1座原料场等18个生产工序,涉及厂区面积达13.5平方公里,是钢铁行业实施的最大规模、产线最多、集成度最高的智慧集控项目。
中冶赛迪基于水土云工业互联网平台的技术积淀,打造一体化智慧管控系统,将复杂的生产过程数字化、生产要素透明化,对厂内物质流、能量流和信息流进行耦合协同,通过工序内流程优化、工序间流程动态匹配,实现钢厂从行政化管控到流程化管控的转变。在马钢炼铁智控中心,仅设置120多个工作岗位,就完成了炼铁全工序的远程生产控制,一期优化200余人,劳动生产率提高了39%,有效降低了生产成本,提升了精益运营水平。
首次实现10公里以上超远距离生产集控,保障安全本质化
马钢炼铁智控中心是中冶赛迪实施的行业首个管控中心搬离厂区内的智能制造项目,铁区原有的46个现场中控室撤销,合并到智控中心进行集中操作,最远控制路由超过18公里,打造了城市钢厂“产城融合”的新模式。
在马钢炼铁智控中心,高炉、原料、烧结、焦化以及各公辅区域有序布置,各操作区域的大屏幕上,实时显示着现场的生产画面,工作人员井然有序地工作,通过观看现场采集的实时画面和数据,便可以及时了解一线的生产状况;一旦生产现场出现异常情况,集控中心就会同时发出报警信号,并通过“掌上工厂”推送到对应人员,以便第一时间进行处理。
实现超远距离的生产操作,首先要解决的是安全保障。中冶赛迪基于60年工程技术积淀,为对生产管控系统的安全、可靠、稳定性进行全面升级,集成了200多套PLC/DCS系统、2000多幅监控画面;通过安全系统设计,保证智控中心的供电安全、控制安全、网络安全、数据安全、应用安全和操作安全。
除了保障整体安全,该中心通过智能化手段,将操作人员从繁杂枯燥的“盯屏幕”任务解脱出来,大大降低了低端重复劳动的强度和高危环境工作压力,提高了钢铁工人的幸福感和获得感。
智能化“最强大脑”,
从经验生产转变为数字化生产
中冶赛迪发挥60余年服务钢铁行业的强大领域知识优势,将钢铁工艺机理与大数据、人工智能、5G技术深度融合,上线了马钢炼铁一体化智能化管控系统,造就马钢炼铁“最强大脑”。
该智能化管控系统汇集了马钢炼铁各大工序的数十万点数据,结合马钢生产管理经验,开发了百余项智能模型应用、数百张全自动报表,通过对数据的深度应用,有效支撑120多个岗位的生产操作,为精细化管理提供科学支撑和辅助决策,实现钢铁生产由经验驱动向数字化、智能化驱动的转变,让工作更简单、决策更精准、管理更方便、组织更简洁和生产更高效。
在马钢炼铁智控中心,中冶赛迪还首次将数十项新研发的智能化技术植入智慧炼铁,进一步提高了生产智能化水平。如,打造智控中心和现场人员的集散联动系统,实现关键岗位的信息共享;打造高炉风口智能诊断系统,对监控视频进行多种异常情况的智能识别分析,促进节能降耗和高效生产。
颠覆传统模式,
由专业化流程化管理取代行政化管理
中冶赛迪水土云工业互联网平台技术的应用,颠覆了传统钢铁企业生产组织和管理模式,让专业化流程化的管理取代行政化的管理,让一体化集控平台取代传统信息化架构下分层分段部署的数十个系统,促进了工序间的横向融合、技术融合、生产融合及管理融合,代表了钢铁智能制造的最新方向。
马钢炼铁智控中心基于冶金工程流程学,系统优化铁区生产管理流程,采用“1+4+N”决策协同模式,即:1个智控中心,涵盖决策支持中心、生产指挥中心、运营管理中心、技术集成中心等4个中心;协同铁区N个生产工序,改变了原来各中控室距离较远、独立运行的局面;各工序操作工人集中办公,跨工序、零距离沟通,促进人力最优化、效率最大化及成本最低化。
面向未来,中冶赛迪将以不断创新升级的智能制造解决方案,推动钢铁全流程智能制造深化落地,为钢铁行业高质量发展做出贡献。
《中国冶金报》(2021年2月4日 04版四版)