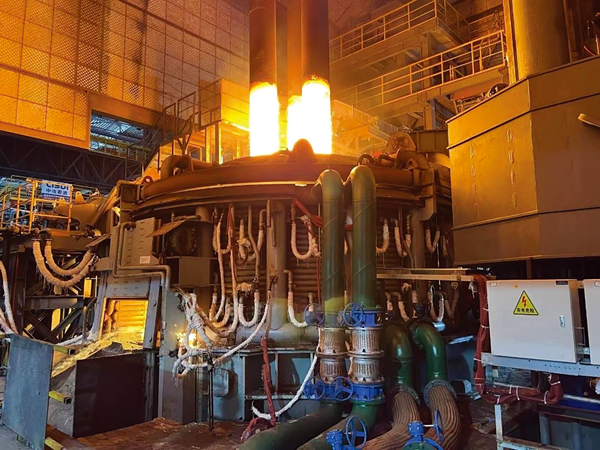
图为中冶赛迪自主研发的阶梯式连续加料电弧炉在四川冶控集团应用。 (中冶赛迪 供图)
本报通讯员 石秋强
2023年4月26日,在云南仙福钢铁第二炼钢厂升级改造施工现场,工程师正在对一座刚刚安装完成的炼钢电弧炉进行调试。这是由中冶赛迪设计,并应用柔性IGBT直流供电、多元炉料结构全余热回收、阶梯扰动涵道废钢预热、多元介质耦合炉底搅拌等多项自主新技术的最新一代绿色高效电弧炉,其投产将推动钢铁行业短流程炼钢技术和装备进步迈上新台阶。
针对国内外全废钢电弧炉在炼钢生产过程中能量消耗高、质量不稳定、二噁英污染等重大关键问题,中冶赛迪历经10余年协同创新,研发了超高功率智能供电、高效深度洁净冶炼、绿色输送废钢预热和高效协同控制集成等绿色高效电弧炉炼钢技术,技术指标达到国际先进水平,在超高功率智能供电和高效深度洁净冶炼方面国际领先,并在国内外广泛推广应用。2020年,中冶赛迪牵头申报的“绿色高效电弧炉炼钢技术与装备的开发应用”项目获得国家科学技术进步奖二等奖。
锚定绿色节能、高效洁净,
创新研发废钢熔炼技术路线
电弧炉炼钢具有流程短、绿色节能等特点,是钢铁工业可循环、绿色化发展的重要方向。但是,长期以来受工艺技术及装备水平等影响,全废钢电弧炉冶炼能量消耗、钢质洁净、环境友好等关键指标难以改善。其集中表现在:成套引进的电弧炉供电系统运行操控模式单一,不能适应我国复杂金属炉料结构,而国产供电装备设计制造技术也未能突破;传统连续加料及预热方式,对废钢质量要求高、但预热效果差,且一直受二噁英污染困扰;未能从根本上解决全废钢生产高品质钢高效去除钢中P、N、O等杂质的技术瓶颈。
中冶赛迪针对国内外全废钢电弧炉炼钢存在的核心技术问题,以电弧炉炼钢绿色节能、高效洁净为目标,探明了全废钢电弧炉生产“废钢输料-预热升温-供能熔化-杂质脱除”的物质能量跨尺度变化特性,提出了废钢绿色清洁使用、快速高效熔炼和产品洁净升级的工艺技术路线,确立了“三个单元、一项集成”的创新研发思路——
以超高功率智能供电、高效深度洁净冶炼和绿色输送废钢预热等新技术为核心,开发了满足复杂炉料结构的超高功率电弧炉智能供电技术及装备,形成了我国超高功率电弧炉供电技术标准体系,打破了国外长期技术垄断;
独创了绿色输送废钢预热工艺,发明了“阶梯扰动”连续加料预热、“烟气分流-自控温”二噁英协同治理和低阻尼高效除尘技术,大幅提升了电弧炉炼钢余能利用水平,实现超低排放;
提出并运用电弧炉炼钢跨尺度物质能量集成方法,创建了电弧炉炼钢多层级信息在线检测和控制系统,实现了绿色高效电弧炉炼钢系统集成联动与高效运行,电弧炉炼钢跨尺度高效协同控制技术集成并实现工业化应用。
攻克传统电炉供电效率低下难关,
开发智能电极调节系统节电成效显著
在复杂炉料结构下稳定保持熔炼过程高电压、长弧供电操作,是电弧炉炼钢提高电能利用率、实现绿色高效节能的关键。长期以来,成套引进的供电系统运行操控模式单一,面对复杂废钢炉料只能采用长时间、低功率因数供电,难以发挥最佳供电效能,造成冶炼效率低、无功损耗大和热量散失严重。
针对上述问题,中冶赛迪研发团队开展了对最佳供电效能的研究和突破,重点对电极调节器性能提升进行研究,多方位调研各个电炉用户的现有电极调节器使用情况。通过研究,该研发团队发现电炉供电系统对提高电炉冶炼效果至关重要,而这部分的研究牵扯到电磁及供电发热等专业方面的研究。为此,该研发团队与西安交通大学、重庆大学等高校联合对于短网系统的电磁场及短网阻抗计算进行了研究。
经过10余年的不懈努力,中冶赛迪成功研发了智能型电极稳弧调节控制系统DMI-AC,开发了信号分布化采集-集中处理-网络数字化传输系统和多策略、多约束优化智能控制技术,有效改善了极限工况下的稳弧控制精度;全废钢冶炼前中期供电功率提高20%~30%,冶炼节奏明显提升,整体热损失降低10%以上,电极消耗减少0.15公斤/吨~0.3公斤/吨;形成了具有企业自主知识产权的电极导电横臂立柱位置自动检测技术和短网优化设计软件,实现了短网系统结构优化与在线监控,三相阻抗不平衡度明显改善(≤2.5%);开发了特大型电弧炉电气运行最佳工作点智能校正专家系统,基于自主研发的电弧炉变压器指数型非线性工作电抗模型,通过多传感器动态跟踪与大数据深度挖掘,实现工作点校正周期小于60ms,超高功率供电功率因数cosφ由0.80~0.85提高至0.85~0.92,电能利用效率提高5%~10%,节电效果显著。
大幅提高废钢预热温度,
高效低成本抑制及脱除二噁英等粉尘
传统电弧炉连续加料及预热技术对废钢质量要求高,预热效果通常仅为200℃~400℃,制约了高温烟气的余能利用;废钢预热温度长期停滞在二噁英合成区范围,二噁英等污染问题难以避免;实现快速高效的连续加料和废钢预热对全废钢电弧炉炼钢能耗和成本控制至关重要。
中冶赛迪研发团队对国内多家电炉生产企业的实地调研和考察,展开废钢预热性电炉的研制工作,在中冶赛迪装备基地制作了试验装置,在中冶陕压建设了工业化样机,最终废钢阶梯加料装置和烟气二噁英处理装置测试数据合格,达到设计要求。
通过此研发和验证,该项目建立了全尺寸废钢料堆空间内烟气流动及交互传热耦合计算模型,探明了高温烟气环境下废钢翻转预热和料层升温特征规律;发明了电弧炉“阶梯扰动”连续加料废钢预热系统,提出并运用阶梯扰动涵道、废钢翻转预热、气流动态密封等创新方法,强化了高温烟气-废钢间热能交换,实现了废钢高宽容性全自动、全密闭连续稳定加料;电弧炉全冷料加料时间缩短至28分钟以内,废钢预热温度提高到500℃~550℃,余能利用量增加25%~30%。
中冶赛迪项目团队研发出了电弧炉炼钢“烟气分流-自控温”和二噁英-粉尘协同净化技术,预热后烟气温度保持在850℃~900℃(维持时间>3秒),二噁英充分裂解后急冷,并结合低温烟气除尘吸附技术,实现了二噁英高效低成本抑制及脱除。经工业试验测试,该技术的二噁英排放<0.1ng-TEQ/Nm3。
广泛开展工程实践,
助力绿色制造
中冶赛迪研发出国际领先的超高功率电弧炉变压器和电极自动调节技术,首次形成了超高功率电弧炉供电技术标准,打破了国外长期技术垄断,强力支撑“中国制造”;开发了适应多元炉料结构的全余热回收、低阻尼除尘、高效急冷二噁英治理、阶梯扰动涵道废钢预热等新技术,系统解决了连续加料、废钢预热、余热利用及废气治理等关键问题;提出了以质量为核心的炼钢洁净生产与绿色制造协同运行新思路;开发了非接触钢液连续测温、炉气成分在线分析、终点预报和成本质量控制软件等,实现了电弧炉炼钢技术集成,进一步提升了电弧炉炼钢运行效率和产品质量,显著降低了生产成本。
中冶赛迪的该项目成果先后在成都冶金、中冶陕压得到应用,并推广至日本共英制钢越南VKS公司(90吨电弧炉)、四川都钢集团电弧炉项目、衡阳钢管电炉项目、山钢日照公司(210吨LF炉)、武钢有限(300吨LF炉)等电弧炉和LF炉炼钢企业,累计交付项目整体或单元技术及装备达80余套,并已出口至土耳其、巴西、印度尼西亚、越南、马来西亚等20余个国家。
其中,四川冶控集团绿色高效电弧炉于2022年6月投入运行,在每天只能生产约9个小时的情况下,吨钢电耗<330kWh、氧气消耗<27Nm3、天然气消耗<1.6Nm3、冶炼周期<36分钟,相关电弧炉炼钢关键技术经济指标已达到了国际先进水平。该项目还采用中冶赛迪具有完全自主知识产权的电炉烟气余热发电技术,电炉吨钢产汽量约130kg,年发电量约2556×104kWh,年供电收益约1151万元,年发电净利润约1000万元,经济效益显著。
《中国冶金报》(2023年05月09日 05版五版)