中国钢铁行业自动化、信息化、智能化进展
殷瑞钰 孙彦广
智能化是当今钢铁工业转型升级和高质量可持续发展的主题之一。新中国成立75年来,伴随着中国钢铁工业由小到大、由弱到强,智能化呈现从生产装备自动化、管理信息化到智能制造的不同层次,为中国钢铁工业发展做出了应有的贡献。
生产装备自动化——
显著提升生产效率和工序过程控制水平促进了钢铁工业规模化发展
钢铁生产装备自动化起源于上世纪50年代,基于自动检测、自动控制、电气传动等技术,与工艺机理和模型结合,实现冶金设备和工序生产过程的自动控制。上世纪70年代,国际上已采用大规模全线自动化的计算机控制。
新中国成立后,国内冶金装置、自动化控制基础还非常薄弱,主要依靠温度、压力和流量等仪表进行手动控制。
20世纪70年代初从日、德、法引进的武钢“一米七”工程,包括从加热炉上料-粗轧-七机架连轧-卷取-运输链全线自动化的两级计算机控制的带钢热连轧厂、计算机控制五机架冷连轧机的冷轧厂、拥有森吉米尔轧机的硅钢厂和计算机控制的板坯连铸机。
20世纪80年代初在上海建设新的宝山钢铁厂,原料场、烧结、高炉、炼钢、焦化、初轧、连轧带钢、无缝钢管以及备用电厂,全部采用先进的EIC(电气仪表计算机)一体化两级自动化系统,主要机组均设有过程计算机,使用数学模型进行优化控制。
20世纪80年代中期以来,在消化吸收国外先进自动化技术基础上,国内进入了自主研发阶段。通过多年的科研攻关、研究开发和工程实践,国内在自动检测、计算机控制、电气传动领域取得了丰硕成果,冶金系列特殊检测装置、大功率交交变频装置填补了国内空白,融自动检测、计算机控制、电气传动为一体的冶金三电自动化系统覆盖了炼铁、炼钢、轧钢各个工序,部分打破了国外垄断,为钢铁工业自动化技术水平提升和全面推广普及做出了贡献。
目前,钢铁企业普遍实现设备的数字化自动控制。将工艺知识、数学模型、专家经验和数字自动化技术相结合,成功应用于炼铁、炼钢、连铸和轧钢等典型工序的过程控制和过程优化,涌现了选矿作业自动控制、烧结机闭环自动控制、高炉专家系统、“一键式”转炉炼钢、精炼炉自动控制、加热炉燃烧优化控制、热连轧模型控制、冷连轧模型控制等具有国际先进水平的科技成果。
冶金自动化应用于钢铁工业,大大减轻了生产人员的工作强度,改善了工作环境,提高了劳动生产率,人均产钢量实现数十倍提升。同时,基于工艺模型的过程控制,提升了炼铁、炼钢、轧钢生产工序的关键工艺变量(成分、温度、尺寸精度和力学性能)的控制水平,在节能、降本的同时,增强了产品质量的稳定性。
企业信息化——
推动钢铁企业精益管理提升企业管控和竞争能力
上世纪60年代,发达国家的钢铁企业纷纷引入计算机管理信息系统。上世纪七八十年代,一些国际知名钢铁企业开发了钢铁企业产销一体化系统。上世纪90年代以后,随着互联网和工业网络发展,企业信息化逐步拓展到生产管控信息化,形成了企业资源计划系统(ERP)和制造执行系统(MES),与工艺装置的过程自动化(PCS)一起构成了完整的三层管控体系。
本世纪初,全球信息化浪潮汹涌,我国提出“以信息化带动工业化,以工业化促进信息化,走新型工业化路子”。其间,钢铁企业信息化显现了前所未有的蓬勃发展新局面。
宝钢股份在创造性地吸收了新日铁公司的扁平化管理模式、消化德国热轧冷轧生产柔性制造系统技术的基础上,采用冶金工艺流程编码技术,打通了从销售到生产的关键流程,集成全流程的质量管理和财务成本管理,建成了综合营销系统。
武钢的整体产销系统涵盖了销售、技术质量、生产、出货、财务和信息作业的一级管理。武钢通过企业的销售合同来贯穿销售、排程、生产、存货、发货的全过程,实时掌握生产进度及实物动态,做到适当的资源调度与安排,实现企业的生产、技术质量、财务等信息作业的一级管理。
经过本世纪初以来的持续发展,信息化在不少重点钢铁企业基本普及:
在生产组织层面,MES(制造执行系统)通过信息化促进生产计划调度、物流跟踪、质量管理控制、设备维护、库存管理水平的提升。EMS(能源管理系统)通过建立能源中心,实现了电力、燃气、动力、水等能源介质远程监控、集中平衡调配、能源精细化管理等功能,涌现了全流程物流件次动态跟踪、炼—铸—轧计划排程、一贯制质量过程控制等具有国际先进水平的科技成果。
在企业运营管理层面,随着企业管理水平的不断提高,ERP(企业资源计划)、CRM(客户关系管理)、SCM(供应链管理)、电子商务等取得成功应用,在更好地满足客户需求、缩短交货期、精细控制生产成本方面发挥了作用。一些大型重点企业建立了集团信息化系统,支持企业一体化采购、销售和多基地生产组织,涌现了产销一体化、供应链深度协同等具有国际先进水平的科技成果。
企业信息化提升了企业集约化经营、扁平化管理、数字化决策和精益管控的能力水平:
首先,我国钢铁企业信息化追求的目标实现了生产从以产品为中心向以客户和市场为中心的转变。满足用户需求,适应市场需要,按照订单组织生产已经成为当前钢铁企业信息系统建设的核心任务。产品交货期相应缩减,有的企业甚至由论月转为论周供货,客户订货的响应速度由过去的数十天加快到数天。
其次,信息化和体制创新、管理创新相辅相成、相互促进。信息化促成了传统产业领域的体制创新和管理创新,企业管理实现了一级财务核算,集中采购、集中仓库管理,统一的生产指挥调度等,显著提高了企业的竞争力。流程再造、机构整合、岗位角色转换、员工素质提高为信息化打下了基础,促进了我国钢铁企业信息化。很多企业由多级财务变成了一级核算。多个科室按照管理流程进行了优化重构,销售、生产、技术质量也实现了一级管理。不少企业还将炼钢厂、热轧厂合并为钢轧厂,全面提高了企业的市场反应能力和用户服务水平。
最后,信息化打破了条条块块的信息壁垒和信息割据,有效解决了信息孤岛现象,在一个全面统一的信息平台上实现了信息共享。生产中的实时成本核算强化了财务的事中监控作用,销售、采购、项目管理和财务系统的集成,强化了企业资金管理,加快了货币回笼和月财务决算。产品标准、技术规范、检验标准等均是成文标准文件,产品检化验和质量异常信息数据高度共享,提升了产品质量PDCA(计划、执行、检查、处理)循环改进能力。
智能制造——
助力我国钢铁工业数字化转型、高质量发展
目前,钢铁工业市场环境、技术环境和社会环境发生了巨大的变化,进入从高速度向高质量发展的数字化转型发展阶段,高端化、绿色化、智能化成为钢铁工业新的发展主题。
钢厂智能化需要采用数字物理系统深度融合的技术路线。该系统以物理系统(工艺流程和装置群)的自组织优化为技术“底座”,以与之相应的数字信息系统为他组织“大脑”,相互作用、相互适应,实现数字信息系统向物理工艺系统赋能,即达成数字信息系统与物理实体系统融合,并能够持续运行,进而实现制造流程(制造工艺流程与相关过程群)整体自感知、自学习、自决策、自执行、自适应。
钢厂智能化的表现形式应该是把数字信息技术系统地融入钢铁制造流程生产运行、运营决策、管理执行的过程中,实现数字化研发和生产、网络协同化制造、一体化生产排程和动态调度、能量流和物质流协同调配、全过程质量管控,实现全流程紧凑连续、动态协同运行,达到节能减排、提质增效的目的。当前,智能制造正在萌发、创新发展的过程中,是钢铁强国、创新发展的重要路径和标志之一,未来,要在党的二十届三中全会精神的指引下,不断探索创新,真正打造新质生产力,助力我国钢铁工业数字化转型和高质量发展。
(殷瑞钰系中国工程院院士;孙彦广系中国钢研科技集团有限公司副总工程师)
史海寻珠①
刘涵清“一米七”工程开中国钢铁自动化之先河
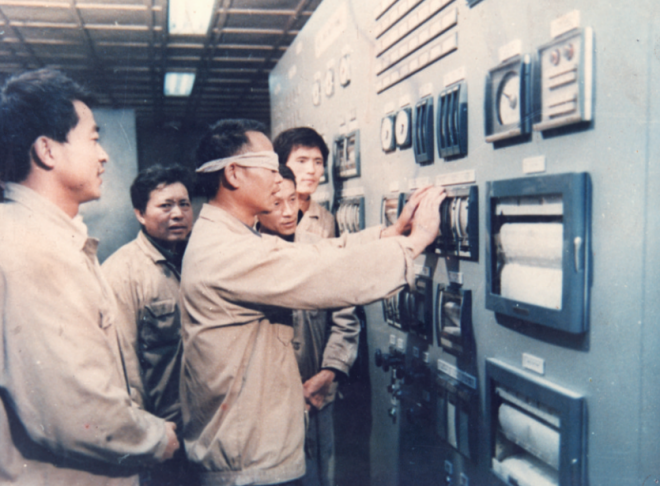
为消化“一米七”轧机技术,武钢人千方百计学技术、练本领。图为武钢职工盲操测试。(武钢 供图)
40多年前,我作为武钢第一任女指挥长,主持“一米七”工程二炼钢厂连铸车间的建成投产,催生了中国第一个全连铸的硕果。
1972年,中央决定引进一批国外先进技术设备,其中包括13套大型化肥设备、4套大型化纤设备、3套石油化工设备、1.7米轧机等。1.7米轧机具有20世纪70年代先进水平,身价也最高,不计国内配套设施,引进费用高达6亿美元,约合40亿元人民币,相当于当时的8亿中国人民每人出了5元钱。“一米七”主体工程包括“三厂一车间”,即热轧带钢厂、冷轧薄板厂、冷轧硅钢片厂和连铸车间,连铸和冷轧设备从联邦德国引进,热轧和硅钢片生产设备从日本引进。该工程从1975年6月正式施工,1978年陆续建成投产。
“一米七”工程具备当时世界先进水平不是假话,从自动化程度来说就了不起,按今天的说法就是智能制造。二炼钢厂连铸车间一进入设备安装阶段我就看出来了,很多配套、辅助的物件都不简单,好比在主体设备上装上了眼睛、耳朵,让铸机能够自动识别钢坯和辊道。到了操作台安装的时候,很多人都惊掉了下巴,全部是电子按钮,所有操作都可以在按钮上完成,这在当时无疑是一个奇迹。
张国文是“一米七”工程热轧项目的中方谈判专家。“一米七”项目启动后,入选为项目组的一员。很多人都知道有一个姓日渡的日本专家在撤离武钢前划过一道开口向下的曲线,意为一旦离开外方专家的支持,“一米七”轧机的生产将掉头向下,却不清楚让这个曲线反过来的人中有多少无名英雄。张国文正是这些英雄中的一员。
日渡走了以后,摆在我们面前的首要难题就是“洋设备吃不惯土面包”。原先不光专家是日本的,吃进去的钢坯也是日本的,轧机开起来就轧有限的几个品种,当然一切顺利。等到日方专家撤了,钢坯也换成了国产的,动不动就卡壳跳闸。
我们采用的方法是调整轧制的参数和模型,自动化那一套已经不好使了,需要从头建模。过程是艰难的,但我们没有被困难吓倒,反而锤炼出了“争气争光争一流”的“三争”精神。暂时放弃自动化是无奈之举,但是很有必要,因为如果不那样轧机就什么也干不了。从积累数据到重新建立轧制模型,武钢人仿佛开了窍,在自动化方面走上了一条不同凡响的自主之路,当时走到了国内前列。
最终,在大家的共同努力下,热轧厂终于可以顺利地“吃下”二炼钢厂连铸车间生产的钢坯!而且轧制的品种越来越多,还可以为后面的冷轧厂和硅钢生产厂两个厂提供质量优良的原料卷,这不是哪一个厂的胜利,而是整个“一米七”工程的胜利。
还有一个关键人物,为武钢“一米七”工程贡献了力量。他就是不久前逝世的张寿荣院士。
1982年,时任武钢副总经理的张寿荣受命主持“一米七”全面达产工作。在他的指导下,1.7米轧机系统开展了外貌、性能、精度和自动化程度“四恢复”,并在此基础上鼓励工人和技术人员消化吸收再创新。武钢二炼钢厂于1985年3月在中国首次实现全连铸,到1985年底,武钢已能生产1.7米轧机系统原设计的全部钢种。1990年,“武钢一米七轧机系统新技术的开发与创新”项目获得了国家科技进步奖特等奖。
不仅如此,“一米七”工程还树立了我国钢铁工业成套引进吸收世界先进技术装备,在全面掌握的基础上不断创新最终实现反向输出的典范。这其中既有工人操作诀窍的总结,也有现场创造发明的成果;既有机械、电气自动化的不断升级,也有基于计算机技术的智能化革新和集成式创新。武钢于上世纪90年代初自行研制成功的APC(高级过程控制)带材纠偏装置技术,成功解决了薄板生产中的跑偏断带问题,1992年被纳入《“八五”国家重点新技术推广项目计划》,并向当时的日本新日铁公司转让4套这种装置。武钢自行研制开发的冷轧带钢生产线防塌卷技术,攻克了国际性技术难题,1993年又一次将该项技术转让给日本。
(本报通讯员程琳整理)
史海寻珠②
阮文杰:南钢智慧运营中心实现跨领域甚至全局寻优
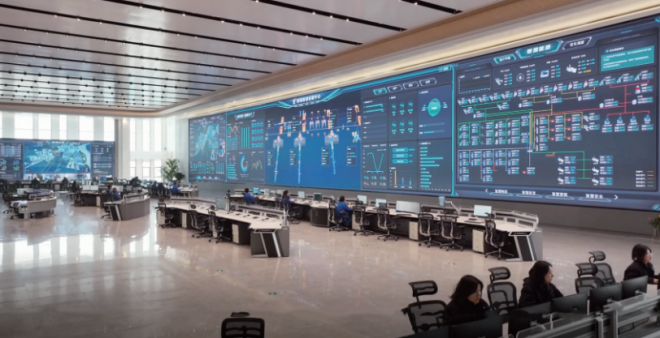
图为南钢智慧运营中心。(南钢 供图)
2021年11月28日,历时475天建设的南钢智慧运营中心正式投用了。该项目荣获2024年冶金科学技术奖特等奖,是行业内首个数字化转型特等奖项目,作为这套系统软件的开发企业——江苏金恒信息科技股份有限公司智能化部副部长,我深感荣耀与欣慰。
它在钢铁行业创造了多项领先:行业首创铁区物料跟踪系统;成为首个覆盖钢铁“研产销”全业务、全链条的集群式一体化的数字运营平台;关键工序数控化率超过80%,连接现场7万多个数据采集点,实现了物质流、信息流、能量流的全要素汇集。“生产全景一块屏,运营管理三张图,要素指标一张表”成为南钢生产管控、协同调度、智慧运营、应急响应4条管理主线的重要支柱。
能够参与这样一个项目,我感到很自豪。回想起来,最难的是项目刚起步的时候,不知道要做成什么样,行业内也没有可借鉴的案例。公司领导几乎每天都带着我们开项目会,一点一点去磨、去讨论,不断地推翻、再优化,像“历劫”一样。
钢铁企业流程长,数据多维高频、非结构化、强业务性、强耦合性等特点导致数据获取难、治理难、使用难,成为该项目实现的最大难点。过去,工厂生产、财务信息、客户管理等诸多部门产生、积累了大量的过程数据,它们都记录着公司的生产和经营状态,但又散落在各个系统里成为“散兵游勇”,没有形成合力。经过持续的数字化建设,南钢建成了自己的全栈式工业互联网,现场织就了一张实时感知网,各类数据上云入湖“、颗粒归仓”。通过连续几场战役,南钢在生产端实现了铁区一体化集控、钢轧分区集控、C2M(用户对制造端)智能工厂,上线了EMS(能源管理系统)和QMS(质量管理系统)。在运营端,南钢有了智慧物流系统、数字研发平台、财务共享中心、一体化招采平台等数字化系统。在销售端,南钢面向客户形成了C2M云商平台、GMS(重工制造业供给体系)产业互联平台。在数据治理体系的支撑下,南钢有了开展全流程数据跟踪、一体化运营和全局寻优的条件。是到钢铁企业全要素集成,把这些海量数据组织起来,结成“军团”释放价值的时候了。就这样,经过无数次的思想碰撞与打磨,南钢智慧运营中心项目应运而生。
通过智慧运营中心项目的建设,南钢形成了“一脑三中心”(智慧运营中心、铁区一体化智慧中心、钢轧一体化智慧中心和能源管控一体中心)的布局,实现了大规模集控、无边界协同、大数据决策、智能化运营的变革。
经过铁区一体化集控中心的全面改造和升级,480名工人脱离了危险的工作区域。因为有了全景式数字驾驶舱,才实现了多岗融合、跨区域可视可控,集约化生产带来了人员作业效率15%以上的提升。
从看不见到看得见,从看不清到全透明,在南钢智慧运营中心联合调度和全局寻优的助力下,整条生产线如同精密的齿轮,相互咬合、有条不紊地运转。仅通过煤气精准调度和发电机组运行模式的优化,就将年度高炉煤气放散率降低到0.23%,实现自发电年均增益超4500万元,这是一项行业领先的成绩。通过对在途物料和铁水罐运输的实时跟踪,南钢智慧运营中心引导各部门协作,在铁运停时费上实现年降本400万元,耐材费用每年也节约了300万元。南钢智慧运营中心以数据支撑物流协同调度、物料全流程跟踪、质量一贯制管理,实现了加工成本下降20%、吨钢质量成本下降10%、吨钢能源综合成本降低2%、产品成材率提升2%。这就是借数据之力实现无边界协同、智能化运营所产生的价值。
从单领域、单工序寻优走向跨领域甚至全局寻优,实现业务流程横向到边、管控纵向到底的多专业、多领域高效协同管理侧的提升是最有价值且具有划时代意义的,这是行业首个以集群式一体化运营管理理念构建的智慧运营中心。正如南钢党委书记、董事长黄一新所说:“未来只有两种企业,数字化企业与非数字化企业。”南钢将继续向智而行,将数据资产凝练为钢铁工业的知识大脑,着力构建面向钢铁制造的行业大模型,拓展小模型应用深度,以大模型+小模型+机理模型耦合应用的能力,赋能“一脑三中心”,持续提升智慧制造、智慧运营能力,实现全领域的业务寻优。
(本报通讯员荣慰整理)
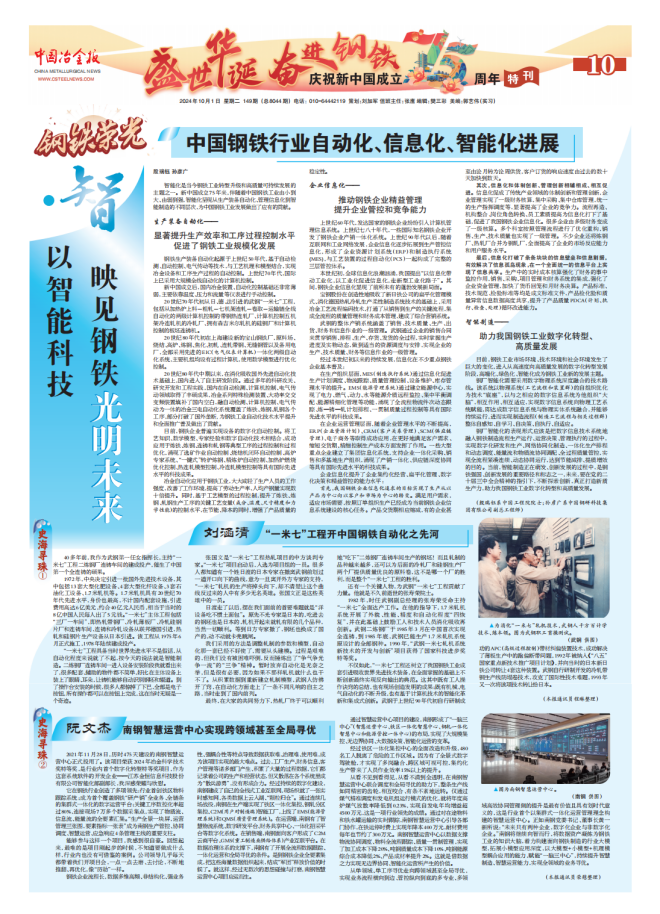