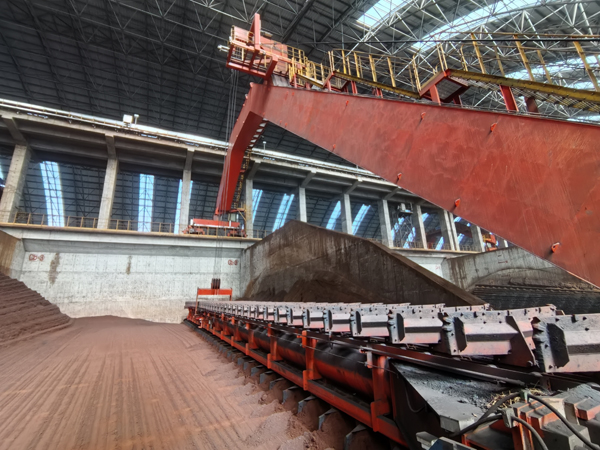
图为本钢智慧料厂的刮板机正在进行无人全自动取料。(彭诚 摄)
本报讯 近日,在本钢北营公司400平方米的“智慧料场”,笔者看见刮板机、卸料机、堆取料机在无人操作的状态下,自动完成卸料、堆料、取料等工艺流程,实现了现场设备智能化全自动作业。
本钢北营公司“智慧料场”于2023年11月份正式投入运行,现场设备包括C型料场卸料机2台、刮板机3台、堆料机1台、混匀库取料机2台。该“智慧料场”创造性地提出了原料场智能管控一体化平台架构及流程优化决策方法,旨在实现原料场从受卸到生产用户的全自动作业。
对此,本钢北营炼铁总厂与中冶赛迪合作开发出智能混匀配料系统、堆取料无人化系统以及数字化料场系统,并结合现场操作实际经验,在三大系统基础上对料场进行无人化、智能化升级改造。同时,该总厂还以国内领先企业为标杆,通过生产和调试的并行推进,最终攻克了堆取料无人化技术、高精度三维图像重构技术等前沿智能化技术应用难题,实现了料场的无人化、智能化全自动作业。
在智能混匀配料系统升级改造中,该总厂用格雷母线实现精准定位,系统控制料车自动堆料,并实时预测混匀矿目标成分,多维立体跟踪混匀配料过程,从而稳定混匀矿成分,提高混匀矿质量,大幅提升作业效率。
在堆取料无人化系统升级改造中,该总厂根据设定工艺参数,结合运动路径解析模型和堆料动作策略模型,实现堆取料机自动对位、自动移位、自动遛垛,整个堆料过程无需人工干预,料场利用率提升20%以上。
据了解,堆取料无人化系统还实现了堆取料机的姿态精确定位、故障自诊断、自动防碰撞、高清监视、远程操控和全自动作业,消除了人工作业的不稳定因素,劳动生产率提升了300%以上。
为打造数字化料场系统,该总厂利用三维激光设备实时扫描料堆轮廓,创新采用图像处理技术和高精度三维图像重构技术,建立实时的料堆三维数字化模型,并结合图像分析模型精确计算料堆体积和重量,实现料场数字化管理和精细化管控,盘库效率提升95%以上。 (何涛)
《中国冶金报》(2025年04月22日 04版四版)